SteriTech sought to enhance its order fulfillment capabilities by integrating its ERP system with a third-party warehousing service. Faced with the challenges of manual data transfer and the risk of errors, SteriTech partnered with Data Stream UK to automate and streamline the process, ensuring accurate and efficient data transmission between systems.
SteriTech, a leading provider of pharmaceutical clean and sterile process solutions, faced the challenge of enhancing its order fulfillment process. To achieve this, they needed to integrate their central ERP system, with a warehousing and fulfillment company. The existing manual process of transferring data between systems was not only time-consuming but also prone to errors, which could lead to inefficiencies and potential disruptions in their supply chain.
Recognising the need for a more streamlined approach, SteriTech partnered with Data Stream to implement a comprehensive data integration solution. Our first step was to work closely with SteriTech’s stakeholders to refine the project’s requirements and develop a data strategy that aligned with their operational goals. The strategy focused on automating the data transfer process to minimise manual intervention and reduce the risk of errors, thereby improving the overall efficiency of order fulfillment.
Next, we assessed the existing data infrastructure and identified that it was not fully equipped to support the seamless integration SteriTech required. Data Stream UK reimagined the infrastructure, designing a solution that combined new custom scripts with SteriTech’s existing database. This approach ensured that we could deliver a cost-effective solution while optimising the infrastructure for the specific needs of the project.
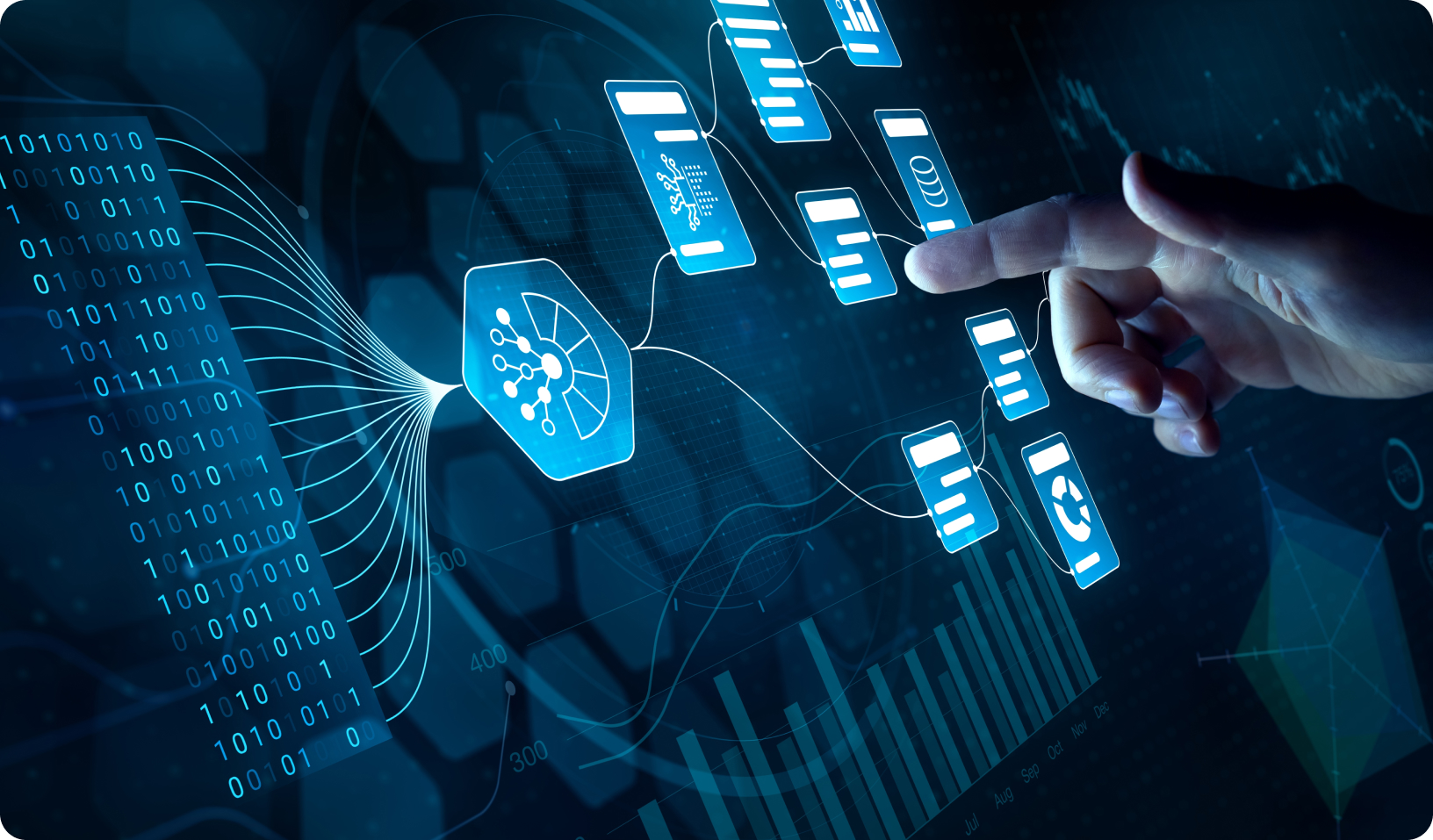
With the infrastructure in place, we concentrated on data quality and analysis, determining the exact data points needed to populate five critical CSV files: product creation templates, sales order templates, and purchase order templates. By extracting real-time data from the SQL database, we ensured that the information transferred was accurate and up-to-date, which was crucial for maintaining smooth operations and compliance with industry standards.
We also focused on ensuring that SteriTech’s team had the necessary skills to support the new integration. By providing targeted training and ongoing support, we made sure that the team could manage the new processes effectively and confidently, contributing to the success of the project.
A significant challenge we encountered was addressing the internal culture at SteriTech. The staff had experienced previous difficulties with system integrations, leading to a cautious attitude toward new technologies. To overcome this, we actively involved key stakeholders from the outset, addressing past concerns and ensuring that the new approach was designed to avoid previous pitfalls. By fostering a sense of ownership and responsibility among the team, we facilitated a smoother and quicker adoption of the new system.
Finally, we addressed data governance by implementing strict protocols to ensure that all data was securely stored, properly managed, and compliant with regulatory requirements. This not only protected SteriTech’s sensitive information but also ensured that the data was accessible and useful to all relevant stakeholders.
Through this structured and comprehensive approach, Data Stream delivered a solution that not only met SteriTech’s immediate need for efficient data integration but also set them up for continued success. The automation of data transfer processes reduced manual effort, minimised errors, and enhanced SteriTech’s order fulfillment capabilities, allowing them to maintain their reputation for delivering high-quality pharmaceutical solutions in an increasingly competitive market.